Custom plastic extrusion designed to your industry needs
Custom plastic extrusion designed to your industry needs
Blog Article
Checking Out the Various Methods and Technologies Behind Plastic Extrusion
The realm of plastic extrusion is a blend of innovation, accuracy, and innovation, crucial to many industries worldwide - plastic extrusion. Advanced machinery, digital controls, and a variety of materials converge in this complicated procedure, producing top quality, durable products. As the market develops, a shift towards lasting products and smart equipment is evident. The adhering to discussion will certainly drop light on these techniques and innovations, while additionally meaning the exciting future leads of this essential manufacturing process.
Comprehending the Essentials of Plastic Extrusion
The process of plastic extrusion, often hailed as a cornerstone in the realm of manufacturing, forms the bedrock of this conversation. Essentially, plastic extrusion is a high-volume production procedure in which raw plastic product is thawed and created right into a continual profile. It's a method commonly used for producing things with a consistent cross-sectional account, such as pipes, window frames, and weather condition stripping. The process starts with feeding plastic products, often in the kind of pellets, right into a warmed barrel. There, it is combined and heated till it ends up being molten. The molten plastic is then compelled through a die, forming it into the desired type as it sets and cools.
The Duty of Various Materials in Plastic Extrusion
While plastic extrusion is a generally made use of method in manufacturing, the products utilized in this procedure considerably affect its final result. Different types of plastics, such as abdominal muscle, pvc, and polyethylene, each lend one-of-a-kind buildings to the end item. Producers should thoroughly take into consideration the residential properties of the material to optimize the extrusion process.
Strategies Utilized in the Plastic Extrusion Refine
The plastic extrusion process involves numerous techniques that are vital to its operation and performance (plastic extrusion). The conversation will begin with a simplified description of the essentials of plastic extrusion. This will certainly be followed by a break down of the process carefully and an exploration of approaches to improve the performance of the extrusion strategy
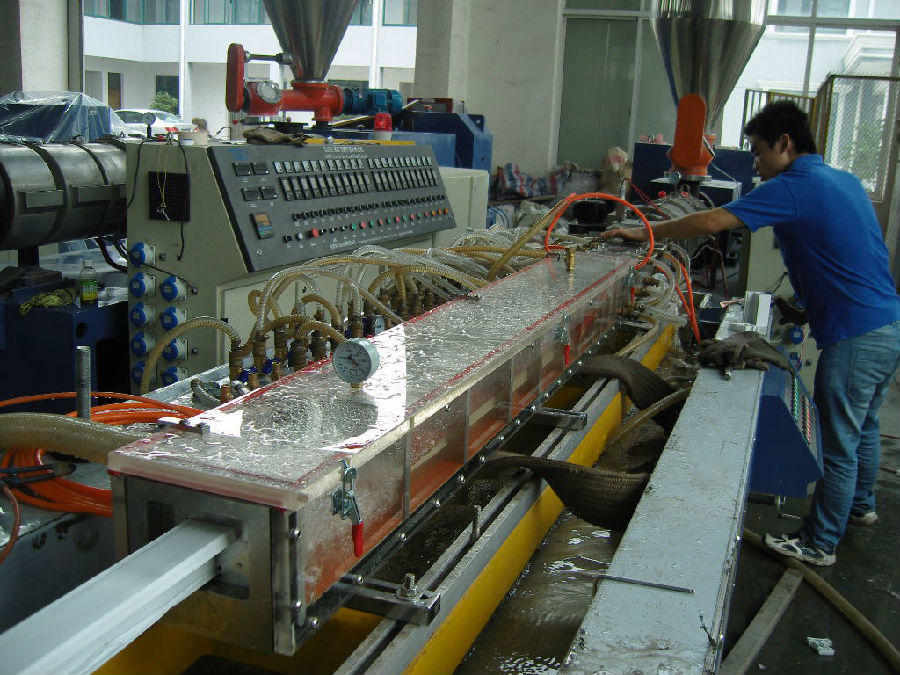
Recognizing Plastic Extrusion Fundamentals
In the world of manufacturing, plastic extrusion stands as a basic process, necessary in the manufacturing of a wide variety of day-to-day items. At its core, plastic extrusion includes transforming raw plastic material right into a continuous profiled form. This is attained by melting the plastic, commonly in the kind of granules or pellets, and compeling it via a designed die. The resulting product is a long plastic item, such as a panel, wire, or pipe finishing, that maintains the form of the die. This economical method is highly versatile, able to develop complex forms and accommodate a variety of plastic products. Basic understanding of these basics enables further exploration of the much more detailed aspects of plastic extrusion.
Detailed Extrusion Refine Break Down

Improving Extrusion Strategy Performance
Effectiveness gains in the plastic extrusion process can dramatically impact both the high quality of the last item and the overall performance of the procedure. Continual optimization of the extrusion strategy is important to maintaining a competitive side. Routine maintenance of extrusion equipment can also minimize downtimes, hence increasing performance.
How Modern technology Is Changing the Face of Plastic Extrusion
The introduction of new modern technology has actually significantly transformed the landscape of plastic extrusion. It has actually caused the advancement of advanced extrusion machinery, which has improved the performance and top quality of the plastic extrusion process. Moreover, developments in the extrusion process have also been driven by technological advancements, using enhanced capacities and flexibility.
Advanced Extrusion Machinery
Revolutionizing the world of plastic extrusion, progressed machinery imbued with cutting-edge technology is introducing a new period of performance and precision. These makers, equipped with cutting-edge attributes like self-regulating temperature level control systems, guarantee optimum conditions for plastic handling, therefore decreasing waste and enhancing product top quality. High-speed extruders, for example, enhance outcome prices, while twin-screw extruders use exceptional blending capabilities, important for creating complicated plastic blends. Furthermore, digital control systems supply extraordinary precision in procedures, decreasing human mistake. Moreover, these makers are developed useful reference for durability, decreasing downtime and maintenance prices. While these improvements are currently impressive, the continual advancement of technology guarantees even better leaps ahead in the field of plastic extrusion machinery.
Advancements in Extrusion Procedures
Using the power of modern technology, plastic extrusion procedures are going through a transformative transformation. Technologies such as computerized mathematical control (CNC) systems now enable even more precision and consistency in the manufacturing of extruded plastic. Automation better improves efficiency, decreasing human mistake and labor expenses. The assimilation of synthetic intelligence (AI) and artificial intelligence (ML) algorithms is reinventing quality assurance, anticipating variances, and enhancing the total performance of extrusion processes. With the development of 3D printing, the plastic extrusion landscape is likewise increasing into new worlds of opportunity. These technological advancements are not just improving the top quality of extruded plastic items but likewise propelling the industry towards a much more sustainable, reliable, and ingenious future.
Real-World Applications of Plastic Extrusion
Plastic extrusion, a effective and functional process, discovers use in many real-world applications. The automobile industry additionally utilizes this innovation to create components like trim and plastic sheeting. The toughness and adaptability of plastic extrusion, paired with its cost-effectiveness, make it an indispensable process across numerous sectors, highlighting its prevalent practical applications.
The Future of Plastic Extrusion: Forecasts and Trends
As we look to the perspective, it ends up being clear that plastic extrusion is positioned for substantial improvements and makeover. Eco-friendly options to standard plastic, such as bioplastics, are additionally anticipated to get grip. These fads indicate a dynamic, evolving future for plastic extrusion, driven by technological innovation and a commitment to sustainability.

Conclusion
In conclusion, plastic extrusion is a complex procedure More Help that utilizes advanced innovation and varied products to develop varied items. As plastic production continues to advance, it stays a vital component of many sectors worldwide.
In significance, plastic extrusion is a high-volume manufacturing process in which raw plastic material is thawed and formed into a continuous profile.While plastic extrusion is a commonly made use of strategy in production, the products utilized in this procedure significantly influence its final output. At its core, plastic extrusion includes changing raw plastic material right into a constant profiled form. It has actually led to the growth of innovative extrusion anchor equipment, which has actually enhanced the efficiency and high quality of the plastic extrusion process.In final thought, plastic extrusion is an intricate procedure that makes use of advanced technology and differed materials to develop varied products.
Report this page